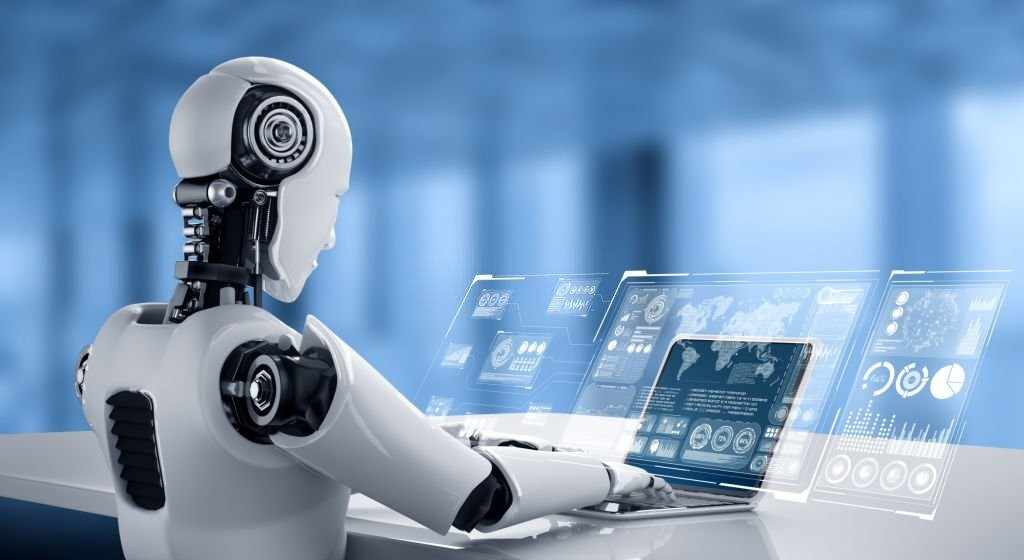
Introduction:
The industrial robot industry is on the cusp of a technological revolution, driven by innovations that are not only transforming manufacturing processes but also enhancing operational efficiency, scalability, and precision. As industries across the globe embrace automation to remain competitive, industrial robots are evolving to incorporate advanced technologies like artificial intelligence (AI), machine learning, connectivity, and cutting-edge sensor systems. These innovations are making robots smarter, more adaptable, and capable of handling increasingly complex tasks. In this article, we will explore the latest technological innovations shaping the industrial robot industry, with a special focus on swarm robotics and distributed task management, AI integration, and other key developments.
Swarm Robotics in Industrial Automation: The Future of Distributed Task Management
Swarm robotics is one of the most innovative concepts that has emerged in the industrial automation sector in recent years. Inspired by the collective behavior observed in nature, such as the movement of ants, bees, or flocks of birds, swarm robotics involves the coordination of multiple robots to work together in a decentralized manner. Unlike traditional robotics, where a central controller is responsible for overseeing all operations, swarm robotics relies on distributed task management, where each robot is autonomous yet able to collaborate with others in real-time.
The application of swarm robotics in industrial automation is creating new possibilities for solving complex problems that would be difficult or inefficient for individual robots to handle. In manufacturing environments, for instance, multiple robots can work together to complete large-scale tasks like assembly, material handling, or sorting. By leveraging swarm intelligence, these robots can perform tasks faster, with greater flexibility, and adapt to changes in real-time.
One of the primary benefits of swarm robotics is its scalability. In traditional automation systems, robots often work in isolation or in small groups, which limits the potential for flexibility. Swarm robotics, on the other hand, enables the deployment of large numbers of robots, each performing specific roles in the task, without requiring extensive coordination or central control. This decentralized approach allows for dynamic reallocation of tasks as production demands change, increasing both efficiency and adaptability.
Swarm robotics also brings new levels of redundancy and fault tolerance to industrial automation systems. If one robot fails or encounters an issue, the rest of the swarm can continue working without disruption, ensuring minimal downtime and improving overall productivity. The ability of robots to reassign tasks among themselves in the event of a failure is a significant advantage, especially in critical manufacturing operations where consistent output is essential.
The potential applications of swarm robotics are vast. In warehouse automation, for instance, multiple robots could work together to transport materials or sort inventory, optimizing space utilization and reducing the need for human labor. In automotive manufacturing, swarm robotics could be used for assembly line tasks, allowing for faster production cycles and greater flexibility. Additionally, the use of swarm robotics in logistics and delivery systems has the potential to revolutionize the way goods are moved within a factory or warehouse environment.
AI-Powered Industrial Robots: Autonomous Decision-Making and Enhanced Efficiency
Artificial intelligence (AI) is another transformative force in the industrial robot industry. AI enables robots to perform tasks with higher levels of autonomy, adapt to changes in their environment, and make real-time decisions without human intervention. The integration of AI into industrial robots empowers them to learn from experience, recognize patterns, and optimize their actions based on the data they collect.
One of the most significant impacts of AI on industrial robots is the enhancement of their decision-making capabilities. AI-powered robots can analyze vast amounts of data from sensors, cameras, and other input devices to make informed decisions on the fly. For example, in quality control, robots equipped with AI can detect defects in products by analyzing visual data and comparing it to established quality standards. These robots can then adjust their actions to address the issue, ensuring that only high-quality products are produced.
Additionally, AI-driven robots can adapt to changing production conditions. In dynamic manufacturing environments, robots often encounter unexpected variations in product specifications, assembly line conditions, or material handling requirements. AI allows robots to respond to these changes without the need for reprogramming or human intervention. This level of adaptability makes AI-powered robots ideal for industries where production needs are frequently modified or where product variety is high.
AI also plays a critical role in improving the safety and efficiency of collaborative robots (cobots). Cobots are designed to work alongside human operators, assisting with tasks that are repetitive or physically demanding. AI enables cobots to recognize and respond to human movements, making the interaction between robots and workers more intuitive and safer. AI-driven cobots can stop or adjust their actions in real-time to prevent accidents, reducing the risks associated with human-robot collaboration.
The use of AI in industrial robots also enhances predictive maintenance capabilities. By continuously monitoring the performance of robots and analyzing historical data, AI algorithms can identify patterns and predict when maintenance is needed. This proactive approach allows for timely repairs or adjustments before a breakdown occurs, minimizing downtime and extending the lifespan of robotic systems.
5G Connectivity and Industrial Robots: Real-Time Communication and Remote Operations
As industrial robots become more advanced, the need for high-speed, reliable communication networks is more critical than ever. The introduction of 5G connectivity is revolutionizing the way industrial robots operate by providing ultra-low latency, higher bandwidth, and more reliable connections compared to previous wireless technologies. 5G enables robots to communicate in real-time with other machines, sensors, and cloud-based systems, optimizing factory operations and ensuring seamless integration of all components in the production process.
One of the most significant benefits of 5G-enabled industrial robots is their ability to transmit and receive large amounts of data with minimal delay. In real-time manufacturing environments, this means that robots can instantly adapt to changes on the production line or respond to external stimuli. For instance, if a machine malfunctions or a new product is introduced into the system, robots equipped with 5G can quickly adjust their actions to accommodate the change without causing delays in production.
The integration of 5G also supports the expansion of remote operations for industrial robots. With 5G connectivity, robots can be operated and monitored from remote locations, making it possible to manage complex manufacturing processes without the need for on-site intervention. This capability is particularly valuable in hazardous environments, where human workers may be at risk. By allowing operators to control robots remotely, 5G ensures that tasks can still be completed safely and efficiently, even in dangerous conditions.
Moreover, the low latency of 5G networks enables AI-powered robots to make decisions in real-time based on data gathered from the factory floor. Robots can instantly communicate with other machines and systems, adjusting their actions based on real-time data and improving overall efficiency. This communication is essential for industries like automotive manufacturing, where precise timing and coordination are crucial to meeting production deadlines.
Vision Systems and Sensors: Enhancing Robot Accuracy and Precision
Machine vision systems and advanced sensors are integral components of modern industrial robots, enabling them to perform tasks with exceptional accuracy and precision. Vision systems, which include cameras, 3D Sensors, and laser scanners, allow robots to "see" their environment and interact with objects in real time. These systems enable robots to perform complex tasks like quality control, object recognition, and sorting with high levels of precision.
Download FREE Sample of Sensors Market
In quality control applications, for example, industrial robots equipped with vision systems can inspect products for defects or inconsistencies. By analyzing visual data, robots can detect even the smallest imperfections and remove defective items from the production line. This level of accuracy is especially important in industries such as electronics manufacturing, where product quality is critical.
Vision systems are also essential for robots that handle delicate materials or products, such as food processing or pharmaceuticals. Advanced sensors and cameras enable robots to detect and manipulate fragile items with care, ensuring that products are not damaged during handling or assembly. These systems can also be used to guide robots in tasks like picking and placing objects, ensuring that items are accurately positioned on the assembly line.
The combination of vision systems and AI-driven analysis allows robots to continuously improve their performance over time. Robots can learn to recognize patterns, identify defects, and optimize their actions based on the data they collect, leading to higher efficiency and better quality control.
Soft Robotics: Flexible Solutions for Complex Tasks
Soft robotics is another area of rapid innovation within the industrial robot industry. Soft robots are made from flexible materials that allow them to perform tasks that traditional rigid robots cannot handle. These robots are ideal for applications where delicate or intricate handling is required, such as food packaging, medical device assembly, or picking up fragile items.
The key advantage of soft robotics is its ability to conform to the shape of objects, allowing robots to handle irregular or delicate materials with greater precision and gentleness. Unlike traditional robots, which are typically made of rigid materials like metal, soft robots use materials such as silicone, rubber, or other flexible compounds. This flexibility makes them more adaptable to different types of tasks and environments.
Soft robots are also lighter and more energy-efficient than their rigid counterparts, making them well-suited for tasks that require dexterity and finesse. For example, in the food industry, soft robots can pick up fruits or vegetables without damaging them, ensuring that products remain intact and suitable for packaging. Similarly, soft robots can be used in pharmaceutical manufacturing, where delicate handling of medical devices and components is crucial.
Modular Robotic Systems: Custom Solutions for Every Industry
The demand for modular and customizable robotic systems is growing rapidly as businesses seek flexible and scalable automation solutions. Modular robots are built using interchangeable components that can be easily adapted or reconfigured to handle specific tasks or production requirements. This modular approach allows manufacturers to design robots that are tailored to their unique needs, without the need for extensive reprogramming or retooling.
The ability to easily modify and expand robotic systems makes them ideal for industries that require frequent changes in production or product specifications. For example, automotive manufacturers can use modular robots to assemble different car models without the need for significant changes to the robot's configuration. Similarly, modular robots can be adapted for various tasks in electronics manufacturing, food production, or logistics, improving overall efficiency and reducing costs.
The scalability of modular robotic systems also makes automation more accessible to businesses of all sizes. Small and medium-sized enterprises (SMEs) can start with a basic robotic system and expand it as their needs grow, without the need for significant upfront investments. This flexibility is one of the key drivers of the growing adoption of robotics across industries.
Conclusion
The industrial robot industry is undergoing a significant transformation driven by a range of technological innovations. From swarm robotics and AI-powered decision-making to 5G connectivity and modular robotic systems, these advancements are reshaping the way industries approach automation. As robots become smarter, more flexible, and more capable of handling complex tasks, their role in manufacturing will continue to expand.
Swarm robotics, in particular, holds the potential to revolutionize industrial automation by enabling decentralized, distributed task management that increases efficiency, scalability, and fault tolerance. When combined with AI, vision systems, and advanced sensors, swarm robots can perform a wide range of tasks with precision and adaptability, enhancing overall productivity and ensuring greater reliability in manufacturing environments.
As the industry continues to evolve, the integration of these technologies will make industrial robots more intelligent, autonomous, and capable of driving the next wave of automation. For businesses that embrace these innovations, the future of industrial robotics promises to be faster, smarter, and more efficient than ever before.
Read the complete blog: https://www.nextmsc.com/blogs/industrial-robots-market-trends
Write a comment ...